What role are 3D laser scanning and mechanical design playing in the carbon capture movement?
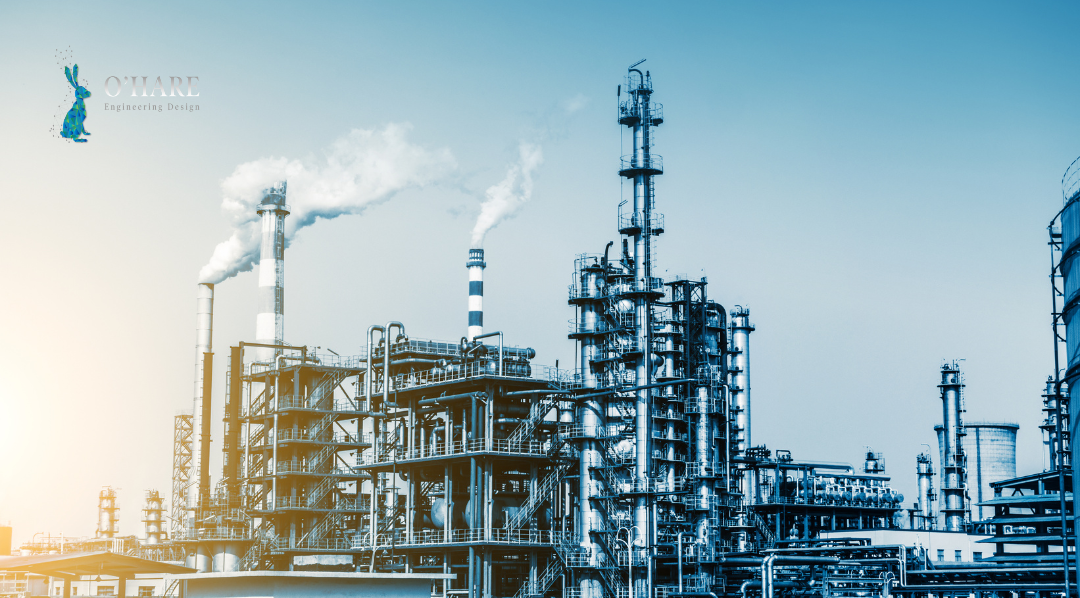
What role are 3D laser scanning and mechanical design playing in the carbon capture movement?
Date: 19th July 2024
The UK has set ambitious goals for reducing its carbon footprint by 2050, and the chemical industry plays a crucial role in achieving these targets.
In 2021 the chemical industry was responsible for around 5% of total net GHG emissions in the EU (ref). But getting this number down can’t just be done with the flick of a switch - it takes a huge amount of engineering, and is seeing lots of chemical plants in the UK adapting their sites to install Carbon Capture and Storage (CCS) systems.
Carbon capture is essentially a giant filtration for the site that traps CO2 emissions, preventing them from contributing to climate change. It’s believed that these filters can capture between 60% to 95% of the CO2 produced by a site (like a power plant) before entering the atmosphere. This captured CO2 can then be permanently stored underground or reused in other industrial processes.
So, how are 3D laser scanning and mechanical design being used in sustainability projects across the UK to transform chemical plants into more carbon-neutral operations?
The challenge of retrofitting existing plants
Integrating carbon capture (CCS) into existing chemical plants is crucial for a low-carbon future, but these facilities pose unique challenges. Their complex layouts, unlike modern plants designed for carbon neutrality, make adding bulky CCS equipment difficult. Traditional measurement methods, reliant on manual processes, are time-consuming and error-prone, further complicated by extensive surveying that disrupts production.
Solving retrofitting challenges with 3D laser scanning
Advanced 3D laser scanning offers a solution for integrating carbon capture systems into existing chemical plants. This technology can be used to create highly accurate digital twins of the space. By scanning a plant, engineers obtain a precise point cloud representation of all its components, including pipes, vessels, and machinery. It also allows the virtual placement of CCS equipment to identify potential space constraints before any physical modifications begin. Real-time simulations can also be run on the digital twin to optimise CCS integration while minimising disruption to ongoing plant operations.
Planning for seamless integration
By having this 3D scan data and using it to develop accurate 3D models of the site, mechanical design engineers can design and integrate the new equipment into and around the existing site. In the case of CCS integration, this meticulous planning involves tasks like designing custom brackets and supports to ensure the capture equipment is securely mounted, and modifying existing piping and ductwork to seamlessly accommodate the capture process. Sometimes it can involve creating entirely new connections for optimal efficiency. By using 3D models within the planning phase of a CCS project, engineers can optimise the placement and layout of the capture equipment, ensuring it integrates seamlessly with the existing plant infrastructure.
Advanced design software empowers mechanical design engineers with a powerful technique called ‘clash detection’. In this process, the 3D model of the capture equipment is virtually placed within a digital twin of the site. This virtual environment acts as a powerful testing ground, allowing engineers to identify any potential spatial conflicts with existing structures or equipment before any physical construction begins. This minimises the risk of unforeseen complications during on-site installation, saving valuable time and resources. Additionally, clash detection helps to identify potential safety hazards that could arise during physical installation, promoting a safer work environment for construction crews.
Furthermore, the iterative design process within the virtual environment allows for continuous refinement and optimisation of the capture equipment integration plan. Engineers can test different configurations and layouts, ensuring the chosen design offers the most efficient use of space, minimises disruption to existing plant operations, and facilitates a smooth and efficient installation process. This translates to reduced project timelines, lower costs, and a minimised risk of delays or complications during the physical integration phase.
The Future of Sustainable Chemical Plants
By combining 3D laser scanning with advanced mechanical design, companies are transforming their operations into more sustainable and environmentally friendly facilities. These advancements not only benefit the environment but also ensure the competitiveness of the UK's chemical sector in the global market. As these technologies continue to develop, we can expect even more efficient and effective methods for capturing carbon emissions and creating a greener future for the chemical industry.
If you found this article interesting, be sure to take a look at our blog about
‘Why are lots of chemical plants in the UK converting to hydrogen?’