Why are lots of chemical plants in the UK converting to hydrogen?
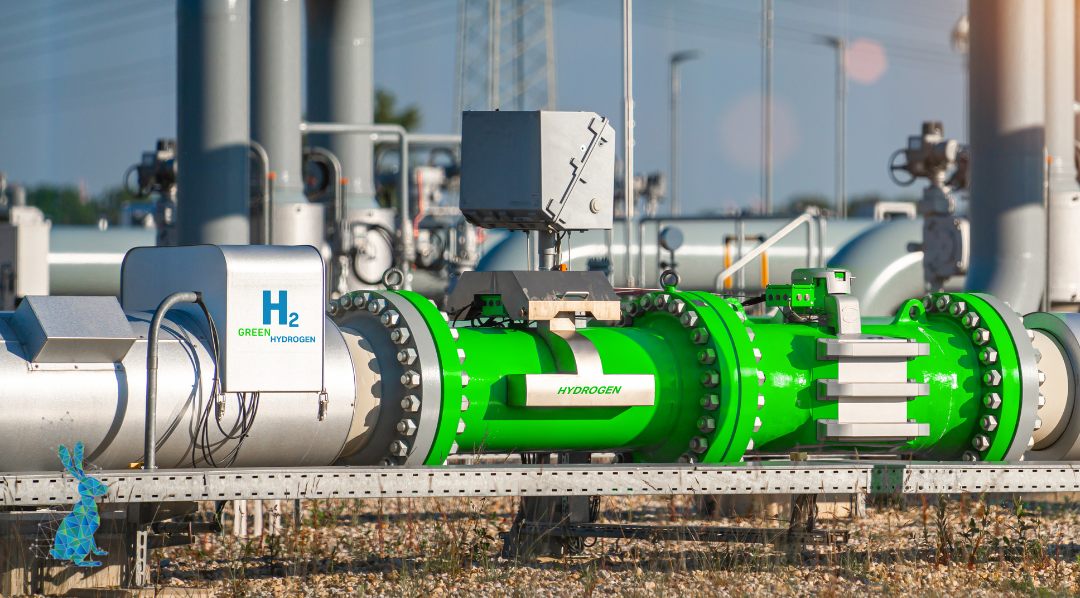
Why are lots of chemical plants in the UK converting to hydrogen?
Date: 23th October 2023
When you think of chemical plants, ‘sustainable’ and ‘low carbon’ aren't usually the first words that come to mind.
In 2021, the chemical industry accounted for around 10% of the UK's total greenhouse gas emissions. But, with the UK's new net zero targets coming into play, many chemical plants are having to make the move towards carbon neutrality, with many opting to make the switch to hydrogen.
There are a number of reasons why chemical plants are converting to hydrogen. The first being that hydrogen is a clean-burning fuel that produces only water vapour when combusted. This makes it an ideal replacement for fossil fuels as it’s a way to reduce their carbon footprint and meet the UK's net zero targets. It’s also more efficient fuel than fossil fuels, so can help to reduce operating costs by extracting more energy from the same quantity and can be used for a variety of purposes in chemical plants, such as generating power, producing steam, and feedstock for chemical processes.
That being said, the overall ‘greenness’ of these sites is directly impacted by the types of hydrogen they are using and in some cases producing.
What are the different types of hydrogen?
There are a number of different types of hydrogen, each with its own environmental impact. The three main types of hydrogen are:
- Grey hydrogen: which is produced from fossil fuels, like natural gas or coal. This is the most common type of hydrogen produced today but it also has the highest carbon footprint.
- Blue hydrogen: Blue hydrogen is also produced from fossil fuels, but the carbon dioxide emissions are captured and stored. This is a cleaner way to produce hydrogen than grey hydrogen, but it’s more expensive.
- Green hydrogen: Green hydrogen is produced from water using renewable energy sources, such as solar and wind power. This is the cleanest type of hydrogen, but it’s also by far the most expensive.
As well as these, there are also a lot of emerging sources of hydrogen that are being developed or are in use in small quantities. These include:
- Pink hydrogen: Pink hydrogen is produced using nuclear power. It is a low-carbon option, but it has the potential to produce radioactive waste.
- Black and brown hydrogen: Black and brown hydrogen are produced from coal and biomass, respectively and have a higher carbon footprint than grey hydrogen.
- Turquoise hydrogen: Turquoise hydrogen is produced from methane using a molten metal pyrolysis process. It is a low-carbon option, but it is still in the early stages of development.
- White hydrogen: White hydrogen is naturally occurring geological hydrogen found in underground deposits. It is still in the early stages of development.
The categories of hydrogen used by UK chemical plants depends on a number of factors, including the availability of renewable energy sources, the cost of hydrogen production, and the specific needs of the chemical process.
Currently, the majority of hydrogen used by UK chemical plants is grey hydrogen. However, many plants are starting the movement towards lower-carbon alternatives like blue and green hydrogen.
What changes to infrastructure will be required for the switch to hydrogen in the UK?
One of the main challenges chemical plants and other industrial facilities face is the need to modify their existing equipment to use hydrogen. Hydrogen has different properties to natural gas, so it can cause problems with some materials used in the existing infrastructure. For example, hydrogen can make steel pipes brittle, making them more likely to crack.
On a larger scale, there are some specific examples of the infrastructure changes that will be required for the switch to hydrogen in the UK including the introduction of a nationwide hydrogen pipeline network, storage facilities, refuelling stations and hydrogen safety systems.
The UK government is working with industry to develop standards and regulations for the use of hydrogen. The government is also providing financial support for hydrogen projects, such as the HyNet project in the North West of England and the Acorn CCS project in Scotland.
The switch to hydrogen in the UK chemical industry is still in its early stages, but a number of major chemical companies have announced plans to convert their plants to hydrogen by 2050. The UK government is also providing financial support for lots of these projects including the development of new hydrogen production technologies, such as turquoise hydrogen.
If you’re part of a transformation project and would like to find out more about how your site could be adapted to support hydrogen usage, get in touch with us today.