Why bother with visualisations in pipework design for chemical plants?
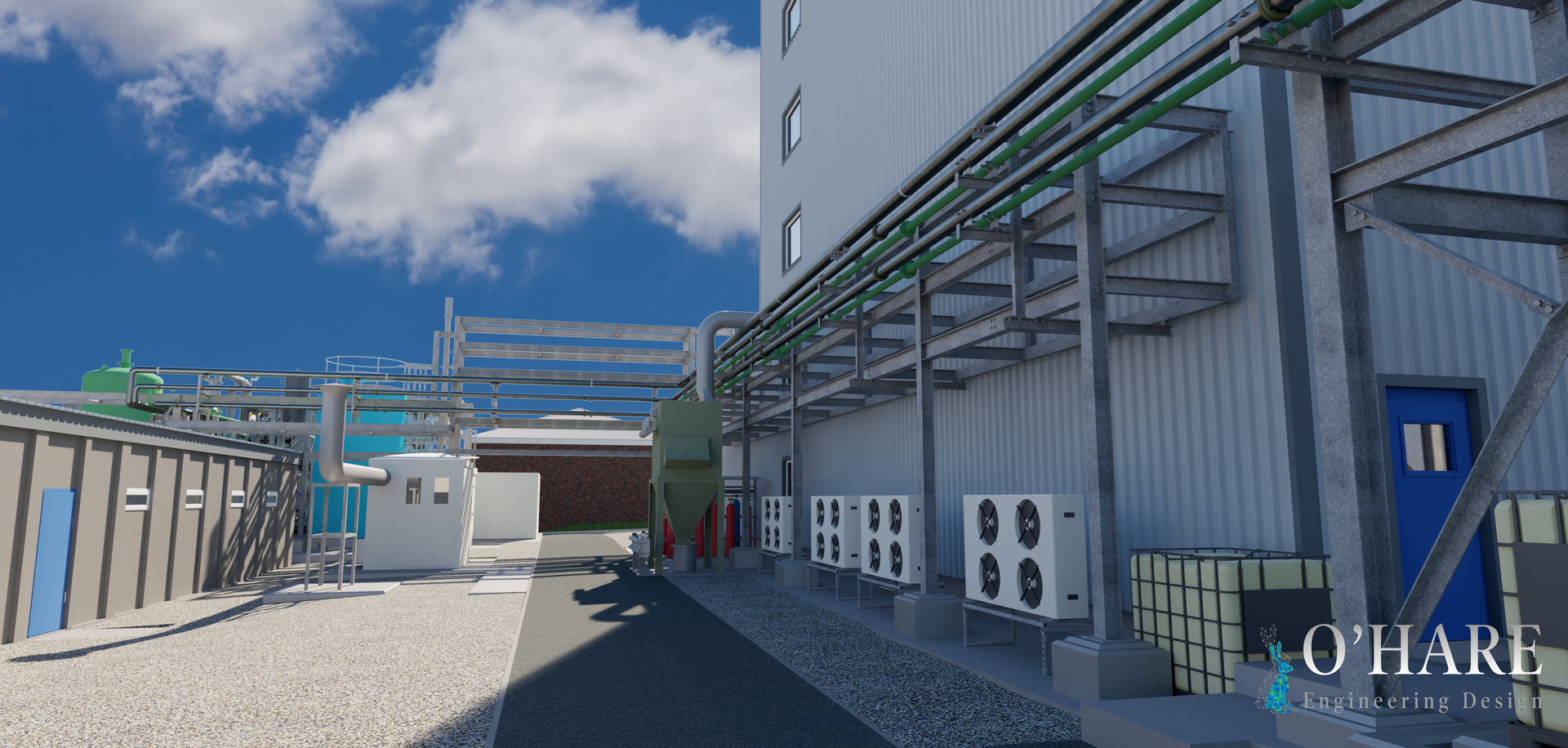
Why bother with visualisations in pipework design for chemical plants?
Date: 29th October 2024
When designing pipework systems that transport hazardous chemicals under high pressure and varying temperatures, safety, efficiency, and cost control are non-negotiables. Mistakes in this critical phase can lead to costly rework, operational inefficiencies, or even dangerous safety incidents.
Traditionally, piping design relied on 2D drawings and manual calculations, but as systems become more complex, so does the need for more advanced tools like 3D modelling, and interactive layouts. These tools allow engineers to create detailed, accurate representations of entire pipework systems, anticipating risks, streamlining installation, and ensuring the system operates correctly from day one.
So, with so many design tools at our disposal, why use visualisations in piping design for chemical plants? And how can they help optimise safety, efficiency, and cost?
Improved understanding of complex systems
Chemical plants often have intricate pipework systems that transport various chemicals under different temperatures and pressures. Visualisations provide a clear, detailed view of these complex systems, making it easier for engineers to understand how different components interact. Instead of relying solely on technical drawings, visual tools give engineers and stakeholders a clearer understanding of the entire network. This clarity ensures everyone is aligned on the project's scope and functionality.
Early detection of design issues
One of the biggest advantages of using visualisations is the ability to spot potential design flaws before they become real-world problems. By using 3D modelling software, design engineers can simulate how a piping system will function under various operating conditions. This allows issues to be picked up early, like pressure drops, inadequate spacing, or material weaknesses. Catching these problems early, before physical construction begins, reduces the likelihood of costly rework and delays later in the project.
Improved communication between teams
Chemical plant design involves collaboration between multiple disciplines - process, mechanical, civil, structural, and safety engineers, to name a few. Miscommunication between these teams can lead to costly errors. Visualisations, such as CAD models or piping and instrumentation diagrams (P&IDs), serve as a universal language that all stakeholders can understand. By providing a visual representation of the system, these tools ensure that everyone involved is on the same page, reducing the risk of misunderstandings.
Using space more efficiently
Maximising space efficiency is essential in chemical plants, where equipment, piping, and safety zones often compete for limited space. Visual models help engineers optimise pipe layouts to ensure smooth operation while avoiding congestion. By visualising the entire system in 3D, designers can identify areas where space is underutilised or overcrowded, leading to more efficient and practical layouts. These optimised designs also ensure that maintenance access is preserved and that the system complies with regulatory and safety standards.
Simulation of real-world conditions
One of the most powerful features of visualisation tools is their ability to simulate real-world operating conditions. Engineers can use these tools to model factors like temperature, pressure, and fluid flow within the pipework. This allows them to predict how the system will perform under various scenarios, helping them to optimise designs for safety and efficiency. By stress-testing designs in a virtual environment, engineers can make data-driven decisions that improve the reliability of the system.
Faster decision-making
The ability to quickly visualise and evaluate design options speeds up the decision-making process. Visual representations enable engineers and stakeholders to assess different scenarios and alternatives in real-time, rather than relying on lengthy technical reports or abstract data. This streamlined approach allows for faster problem-solving and quicker project milestones, which is essential in today’s fast-paced industrial environments.
Cost savings
Perhaps one of the biggest benefits of using visualisations is the cost savings they can provide. Identifying and addressing design flaws before construction begins leads to fewer on-site changes, reducing labour costs and material waste. Additionally, optimised designs can lead to more efficient use of resources, further lowering project expenses. By minimising errors and maximising efficiency, visualisations help companies stick to their budgets while delivering high-quality results.
Incorporating visualisations into the pipework design process for chemical plants is no longer an option but a necessity. From enhancing understanding and communication to optimising layouts and reducing costs, the benefits are clear. By leveraging tools like 3D modelling, and real-world condition testing, engineers can create safer, more efficient, and more reliable systems.
At the end of the day, visualisations help bridge the gap between design concepts and practical implementation, ensuring that chemical plants operate smoothly and efficiently. As technology continues to evolve, we can expect visualisations to play an even more central role in the future of pipework engineering.
To find out more about our visualisation and 3D modelling services,
download our free brochure.